PCB Quality Policy
Our Multifaceted Quality Assurance Program:
- Each of our production process work instructions provide the acceptance and rejection criteria for each of the 90 plus processes in fabricating your circuit board. In addition there are “first article” requirements for a number of steps throughout the course of the manufacturing process.
- Customer specifications and drawings follow along with each order as part of the traveler that accompanies all orders – Small quantity or production PCBs.
- IPC Class 2 provides the default in the event that you do not assign a particular requirement.
- The final step prior to shipping our boards is a well defined final inspection. Each of our orders goes through a C=0 random sampling for determining that the holes and dimensions for each part number are within tolerance.
- Once the order has passed the dimensional check it is scheduled for electrical test if you have requested it.
- The last step for each order is a 100% visual inspection. Each part is checked for workmanship, quality, cleanliness and a number of other attributes before the boards are packaged for shipping.
There are a number of other inspection points that we require throughout the process that we use to verify the acceptability of the panels.
All inner layer cores pass through Automated Optical Inspection prior to being laminated into a multi-layer board. We use cross section analysis to verify plating thickness on the surfaces as well as in the hole walls.
Weight-gain coupons, backlight inspections, visual and magnified inspections of trace width and spacing, drill, image and mask registration as well as a number of tooling checks are done on an order by order basis.
GreenPCB quality system is a compilation of all of these inspection points and more. We work hard to “Make it Right the First Time”!
Also GREENPCB passed the following certification :
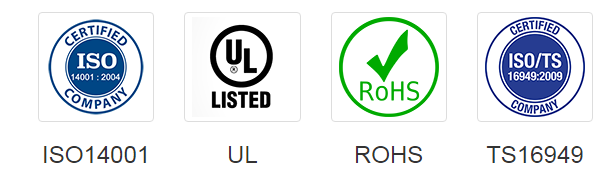